Appliance Manufacturer
Precision Bending has worked with customers in appliance manufacturing for many years. As appliances become more complex, creating custom bending and having flexible production is more important. That change means we can provide the best service for you.
Using CNC benders, Precision Bending strives to provide great engineering input and make our production more flexible to meet manufacturing needs.
Our bending machines are equipped for bending radius change, and die changes. We also have a thorough review and inspection process to ensure the quality you need.
Tube Bending Process for Appliance Manufacturers
Tube bending is a crucial process in appliance manufacturing, especially for products like refrigerators, air conditioners, and washing machines, where precise tube formations are needed for efficient operation. The process involves shaping metal tubes into various angles and curves without compromising their structural integrity.
The first step in tube bending is selecting the right material, typically metals like aluminum, copper, or stainless steel, known for their durability and resistance to corrosion. The tube is then measured and cut to the required length before being placed into a bending machine.
There are different methods for tube bending, each suited for specific applications. The most common are rotary draw bending, roll bending, and mandrel bending. Rotary draw bending is popular for its precision, as it uses a fixed radius die to create tight, consistent bends. Roll bending, on the other hand, is ideal for larger, gentler curves, often used in larger appliances. Mandrel bending, which inserts a mandrel into the tube, helps maintain the tube's diameter during the bending process, reducing the risk of kinks or deformations, making it perfect for thin-walled tubes.
Throughout the process, careful attention is given to avoid defects like wrinkling, flattening, or cracking, which could affect the performance of the appliance. Quality control checks ensure that each bent tube meets the specific requirements, maintaining the integrity and efficiency of the final product. This meticulous process is essential for manufacturing reliable, high-performing appliances that consumers trust.
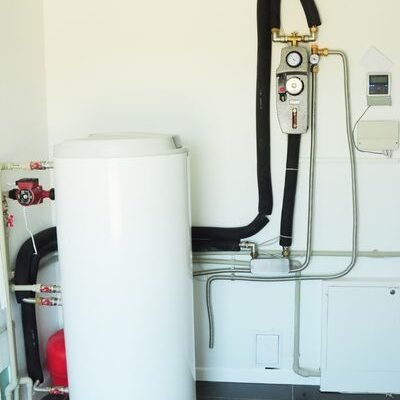
Need help with a project?
Our team of experts can help with engineered solutions.
Our Services
We offer fabrication services for tubing and pipe. Precision Bending has experience in automotive, appliance, plumbing, and other industrial requirements. As a tubular specialist, we offer bending, compound bending, bend-on-bend, flaring and expanding services.
With more than 350 bending tools in our factory, our tube bending capabilities are endless. If you have a tough specification, our engineering team will work with you to find the best solutions. Our capabilities include:
PRECISION
TUBE BENDING
Our in-house precision tube bending including the capability to create fixtures, tools and gauges that produce and check the critical attributes of your part. Our proven process ensures any tubular part fits and performs as designed.
Many parts need to integrate stampings, machined parts and castings, and we support a variety of specialty operations. We manufacture parts with adapters or fittings needing welding or brazing, and pressure test the entire assembly.
ENGINEERING AND
DESIGN CONSULTATION
We have unmatched custom bent tubing knowledge and provide world-class tube bending. We work with clients to engineer and design complex parts to work for your project while maintaining sound structural integrity.
Although we manufacture complex parts, but we make working with our team easy. Get details about our process for partnering with customers on tube bending projects including specification, design, material selection and tube bending costs.