Automotive Tubing
The automotive industry has strict standards that can be met by Precision Bending Technology.
Tube components on these applications are often well concealed but nevertheless critical. Aside from the obvious accuracy and on time delivery requirements, we incorporate full material traceability and product marking.
With our ISO 9001 certification, you can be assured that every tube product and assembly is held to the strict quality processes that we follow.
We understand that automotive products need to be reliable because they provide critical applications. Although we prefer to be involved at the design stage, we are often called upon to produce bend forms that other companies cannot successfully achieve.
Our extensive range of tooling, highly skilled workforce and wide range of checking and inspection capability means that we can be relied upon for the most exacting of tube forms and tube assemblies.
Key Considerations for Automotive Tube Bending
Material & Alloy Selection
Choose tubing alloys that balance strength, corrosion resistance, and formability. Different alloys respond differently to bending processes, so material choice directly dictates bend radii and lubrication requirements.Wall Thickness vs. Bend Radius
Maintaining the correct centerline bend radius to avoid wrinkling, flattening, or kinking. This consideration is especially critical for thin-wall exhaust and fuel lines. If there is a tighter radii, the process may require mandrel tooling, or boosted pressure to preserve cross-sectional integrity.Tooling & Machine Capability
Precision bent components—such as brake or HVAC lines—often rely on CNC multi-stack benders. It is important to compensate with the correct positional tolerances.Process Lubrication & Cleanliness
Select compatible lubricants (e.g., chlorinated oil, synthetic ester) that reduce galling and die wear. It is also important these lubricants do not leave residues that impede downstream welding, brazing, or coating.Inspection & Quality Control
Using inline laser or vision inspection systems to monitor ovality, wall thinning, and true-position of bent segments. It is important to verify that every bend meets OEM dimensional and performance specs.
These five factors—material behavior, geometry limits, tooling strategy, lubrication cleanliness, and rigorous quality control —work together to deliver repeatable, high-precision bends that meet automotive durability and safety requirements.
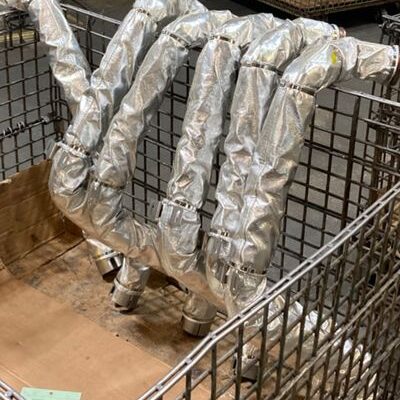
Need help with a project?
Our team of experts can help with engineered solutions.
Our Services
We offer fabrication services for tubing and pipe. Precision Bending has experience in automotive, appliance, plumbing, and other industrial requirements. As a tubular specialist, we offer bending, compound bending, bend-on-bend, flaring and expanding services.
With more than 350 bending tools in our factory, our tube bending capabilities are endless. If you have a tough specification, our engineering team will work with you to find the best solutions. Our capabilities include:
PRECISION
TUBE BENDING
Our in-house precision tube bending including the capability to create fixtures, tools and gauges that produce and check the critical attributes of your part. Our proven process ensures any tubular part fits and performs as designed.
Many parts need to integrate stampings, machined parts and castings, and we support a variety of specialty operations. We manufacture parts with adapters or fittings needing welding or brazing, and pressure test the entire assembly.
ENGINEERING AND
DESIGN CONSULTATION
We have unmatched custom bent tubing knowledge and provide world-class tube bending. We work with clients to engineer and design complex parts to work for your project while maintaining sound structural integrity.
Although we manufacture complex parts, but we make working with our team easy. Get details about our process for partnering with customers on tube bending projects including specification, design, material selection and tube bending costs.