Automotive Tubing
The automotive industry has strict standards that can be met by Precision Bending Technology.
Tube components on these applications are often well concealed but nevertheless critical. Aside from the obvious accuracy and on time delivery requirements, we incorporate full material traceability and product marking.
With our ISO 9001 certification, you can be assured that every tube product and assembly is held to the strict quality processes that we follow.
We understand that automotive products need to be reliable because they provide critical applications. Although we prefer to be involved at the design stage, we are often called upon to produce bend forms that other companies cannot successfully achieve.
Our extensive range of tooling, highly skilled workforce and wide range of checking and inspection capability means that we can be relied upon for the most exacting of tube forms and tube assemblies.
Tube Bending Process for Automotive Parts
Tube bending is a critical process in the manufacturing of automotive parts, playing a key role in producing components like exhaust systems, brake lines, and fuel lines. The process demands high precision and consistency, as the tubes must fit within tight spaces and maintain their structural integrity under various conditions.
The tube bending process begins with selecting the appropriate material, often metals like steel, aluminum, or titanium, chosen for their strength and durability. The selected tube is then cut to the required length and prepared for bending. Automotive parts often require tubes to be bent at complex angles, so the process must be carefully controlled to meet exact specifications.
Several methods are used in tube bending for automotive parts, with the most common being mandrel bending, rotary draw bending, and roll bending. Mandrel bending is frequently employed when tight radius bends are needed, as it involves inserting a mandrel into the tube to prevent it from collapsing or wrinkling. This method ensures the tube maintains a uniform diameter, which is crucial for fluid and exhaust flow in automotive systems.
Rotary draw bending is another popular technique, particularly for creating precise bends with a consistent radius. This method is highly accurate, making it ideal for producing parts that must fit perfectly within the vehicle's design. Roll bending is used for larger, more gradual bends, typically in larger vehicle components.
Quality control is paramount throughout the process, as any defects in the bends can lead to performance issues or failures in the vehicle. Each bent tube undergoes rigorous inspection to ensure it meets the strict standards required for automotive applications, ensuring safety and reliability on the road.
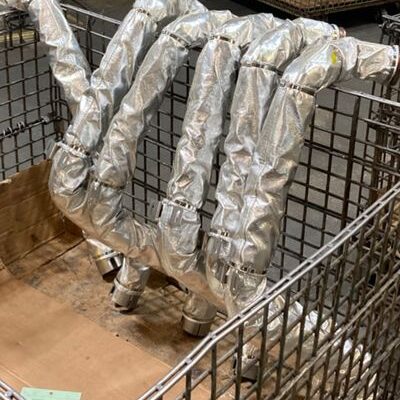
Need help with a project?
Our team of experts can help with engineered solutions.
Our Services
We offer fabrication services for tubing and pipe. Precision Bending has experience in automotive, appliance, plumbing, and other industrial requirements. As a tubular specialist, we offer bending, compound bending, bend-on-bend, flaring and expanding services.
With more than 350 bending tools in our factory, our tube bending capabilities are endless. If you have a tough specification, our engineering team will work with you to find the best solutions. Our capabilities include:
PRECISION
TUBE BENDING
Our in-house precision tube bending including the capability to create fixtures, tools and gauges that produce and check the critical attributes of your part. Our proven process ensures any tubular part fits and performs as designed.
Many parts need to integrate stampings, machined parts and castings, and we support a variety of specialty operations. We manufacture parts with adapters or fittings needing welding or brazing, and pressure test the entire assembly.
ENGINEERING AND
DESIGN CONSULTATION
We have unmatched custom bent tubing knowledge and provide world-class tube bending. We work with clients to engineer and design complex parts to work for your project while maintaining sound structural integrity.
Although we manufacture complex parts, but we make working with our team easy. Get details about our process for partnering with customers on tube bending projects including specification, design, material selection and tube bending costs.