Heavy Equipment
Any product with an engine requires tubing to convey exhaust gases, intake air, hydraulic fluid, fuel and often compressed air from the turbocharger to the charge air cooler.
Precision Bending was asked to product the tubes are typically produced this assembled tube for a manufacturer.
The requirements for these products are stricter with Tier 4 emission requirements. We created a tube coupling system that had low leakage vibration isolation, flexible hose and high levels of cleanliness.
To ensure compliance and remove dust, Precision Bending Technology cleaned all Tier 4 tubes to the new requirements and packages them in a heat sealed bag to ensure a perfectly clean tube is delivered to the customer.
Heavy Equipment Tube Bending
Tube bending is an essential process in the manufacturing of heavy equipment, where robust and durable components are required to withstand extreme conditions and heavy loads. This process is critical in forming hydraulic lines, structural frames, and exhaust systems for machinery used in construction, mining, and agriculture.
The tube bending process for heavy equipment begins with selecting the appropriate material, typically high-strength steel or alloy, known for their ability to endure harsh environments and heavy use. The selected tube is then cut to the desired length and prepared for bending. Given the large-scale and heavy-duty nature of these machines, the tubes often need to be bent into complex shapes and angles while maintaining their structural integrity.
Several methods are employed in tube bending for heavy equipment, including mandrel bending, rotary draw bending, and induction bending. Mandrel bending is used when the tube requires a tight radius bend without compromising the internal diameter, which is crucial for maintaining fluid flow in hydraulic systems. Rotary draw bending provides high precision, making it suitable for components that need to fit within specific design parameters. Induction bending is particularly useful for large-diameter tubes, where it uses electromagnetic induction to heat a section of the tube before bending, allowing for smooth, controlled bends in thick-walled tubes.
Throughout the process, strict quality control measures are implemented to ensure the bends are free from defects like cracking or wrinkling, which could compromise the equipment's performance. The final bent tubes are rigorously tested to meet the high standards required for heavy equipment, ensuring they can withstand the demanding environments in which they will operate.
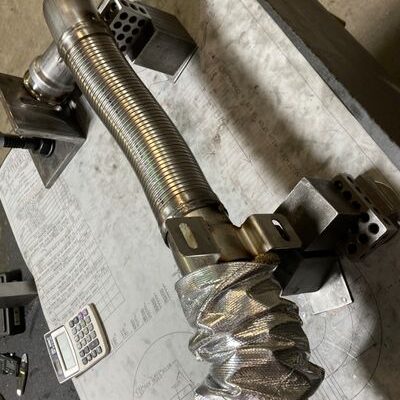
Need help with a project?
Our team of experts can help with engineered solutions.
Our Services
We offer fabrication services for tubing and pipe. Precision Bending has experience in automotive, appliance, plumbing, and other industrial requirements. As a tubular specialist, we offer bending, compound bending, bend-on-bend, flaring and expanding services.
With more than 350 bending tools in our factory, our tube bending capabilities are endless. If you have a tough specification, our engineering team will work with you to find the best solutions. Our capabilities include:
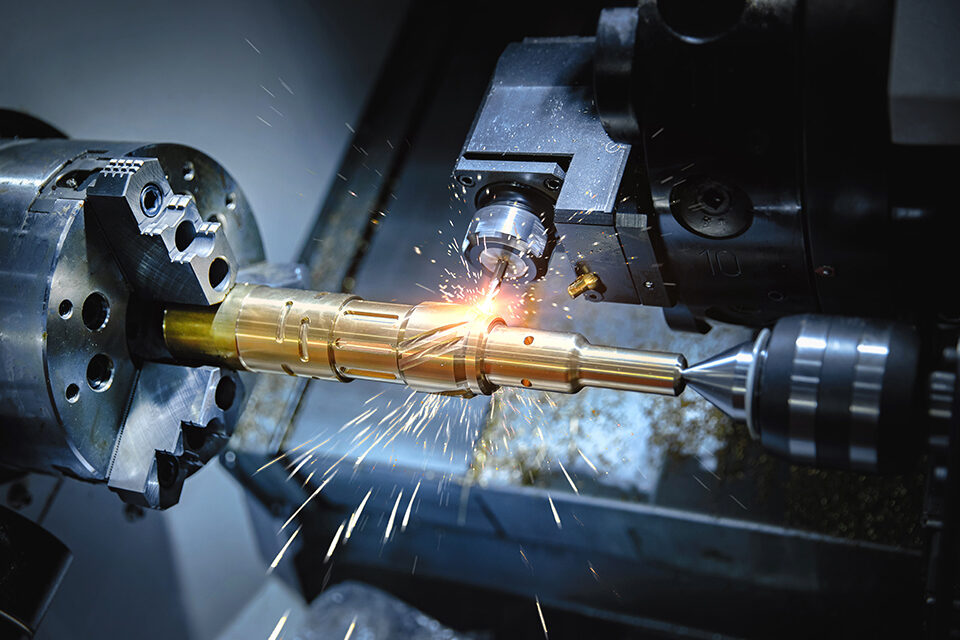
PRECISION
TUBE BENDING
Our in-house precision tube bending including the capability to create fixtures, tools and gauges that produce and check the critical attributes of your part. Our proven process ensures any tubular part fits and performs as designed.
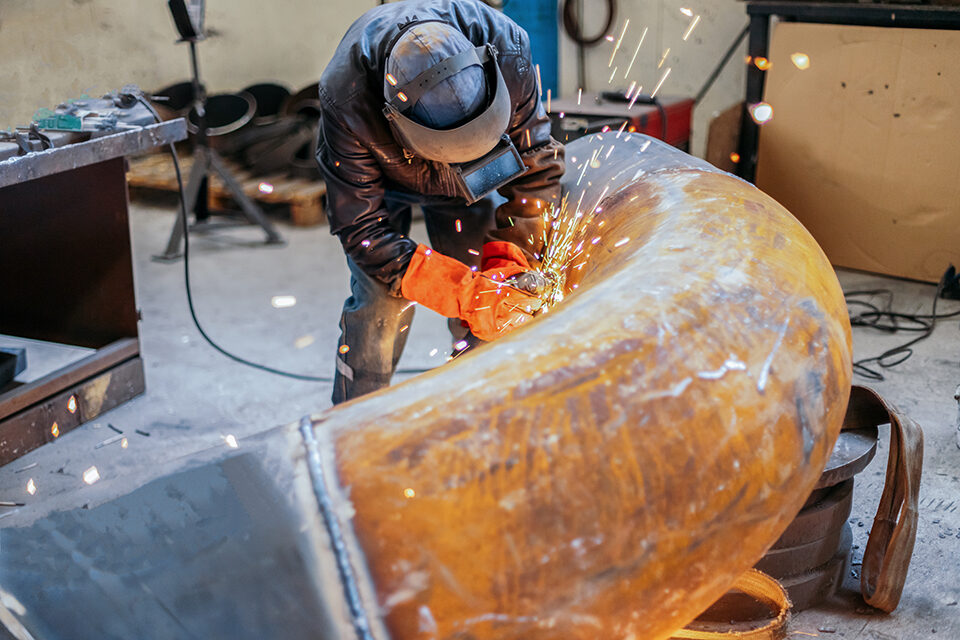
Many parts need to integrate stampings, machined parts and castings, and we support a variety of specialty operations. We manufacture parts with adapters or fittings needing welding or brazing, and pressure test the entire assembly.
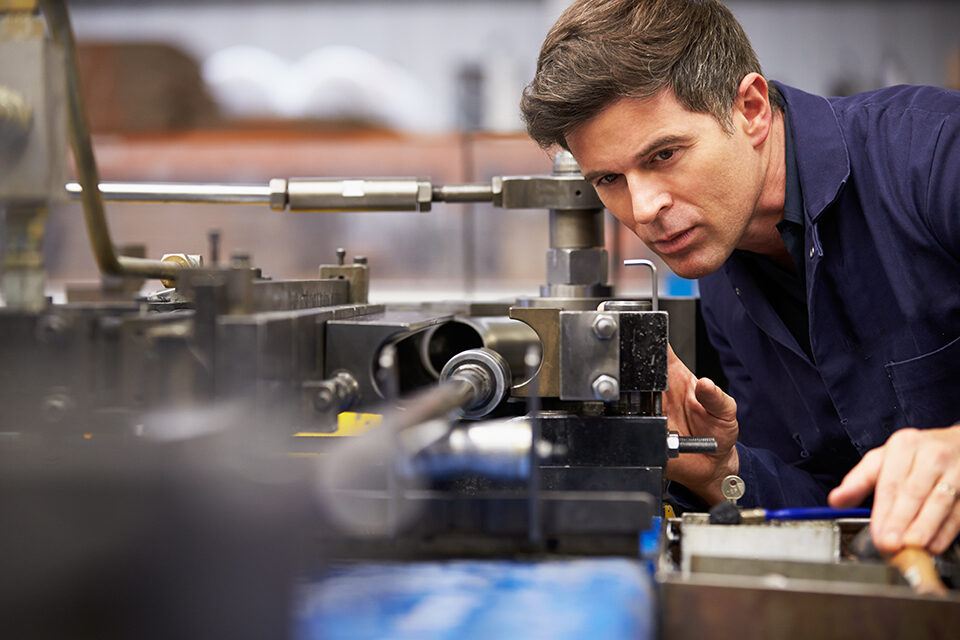
ENGINEERING AND
DESIGN CONSULTATION
We have unmatched custom bent tubing knowledge and provide world-class tube bending. We work with clients to engineer and design complex parts to work for your project while maintaining sound structural integrity.
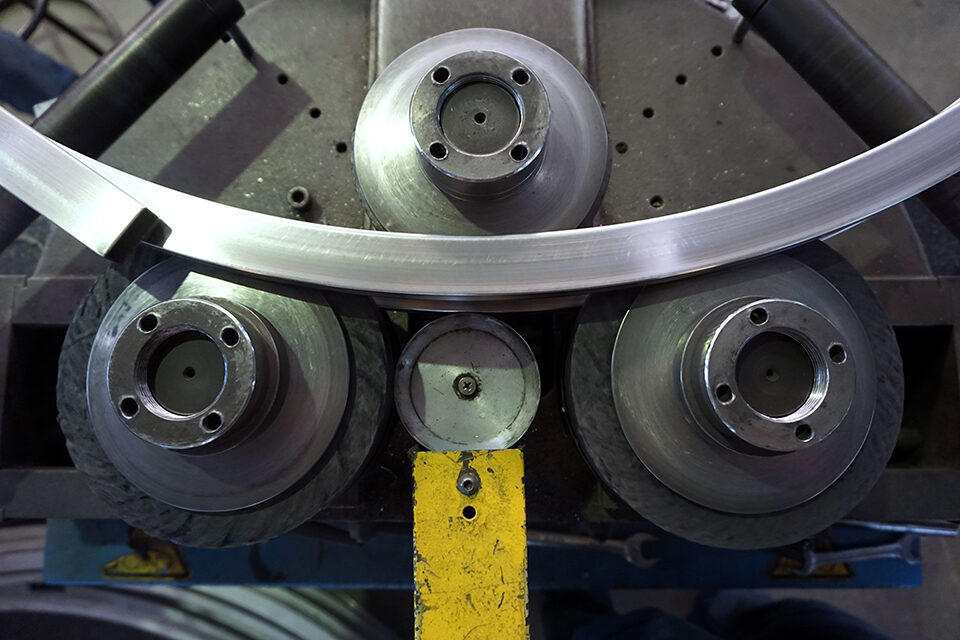
Although we manufacture complex parts, but we make working with our team easy. Get details about our process for partnering with customers on tube bending projects including specification, design, material selection and tube bending costs.