7 Considerations for Custom Tube Fabrication Projects
If you are working on a project, you might be able to use a standard tube to fit and perform for your application. You might be considering a custom tube fabrication. It is a great option, but you need to pick the right partner because custom tube fabrication presents several challenges due to the precision and complexity involved in the process.
Here are some of the main difficulties to think about and ask when vetting a precision bending partner:
1. Material Selection and Handling
Material Properties: Different materials have unique properties such as tensile strength, ductility, and corrosion resistance. Choosing the right material that meets the design specifications and end-use requirements is critical.
Handling and Storage: Some materials require special handling and storage conditions to prevent damage or degradation, such as stainless steel, which can be susceptible to contamination.
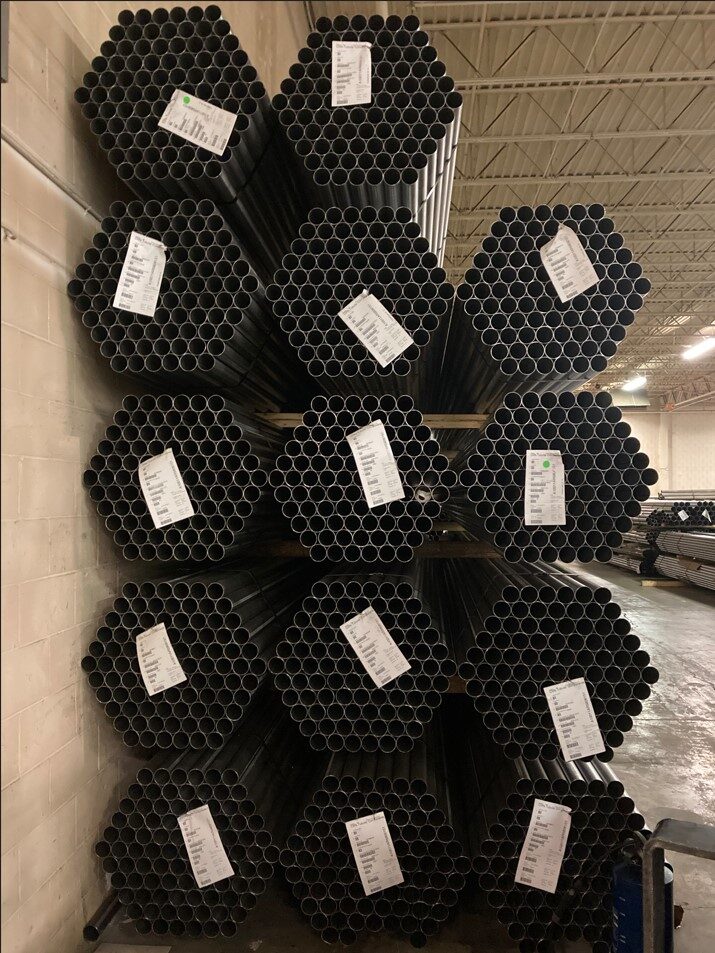
2. Design Complexity
Complex Geometries: Fabricating tubes with complex shapes, bends, and curves can be challenging and often requires specialized machinery and expertise.
Tolerances: Maintaining tight tolerances is crucial in custom tube fabrication, especially for applications where precise dimensions are essential, such as in aerospace or medical devices.
3. Manufacturing Processes
Cutting and Machining: Accurate cutting and machining to achieve precise lengths and end shapes can be difficult, especially for hard or brittle materials.
Bending and Forming: Achieving the desired bend radius and angle without causing wrinkles, flattening, or other deformities requires precise control and high-quality equipment.
Welding and Joining: Ensuring strong, clean welds or joints, particularly in thin-walled tubes, is challenging and requires skilled operators and advanced techniques such as TIG welding.
4. Quality Control
Consistency: Maintaining consistent quality across multiple units, especially in high-volume production, can be challenging.
Inspection: Thorough inspection methods are needed to detect defects such as cracks, voids, or dimensional inaccuracies. This often involves non-destructive testing techniques like X-ray or ultrasonic testing.
5. Tooling and Equipment
Customization: Custom tube fabrication often requires specialized tooling and fixtures, which can be expensive and time-consuming to design and produce.
Maintenance: Regular maintenance and calibration of machinery and tools are necessary to ensure precision and reliability.
6. Cost and Time
High Costs: Custom fabrication is generally more expensive than standard production due to the specialized processes, materials, and expertise required.
Lead Time: The time needed for design, prototyping, and production can be longer, particularly for complex or highly customized projects.
7. Regulatory Compliance
Standards and Certifications: Adhering to industry standards and obtaining necessary certifications can be a complex and stringent process, particularly in regulated industries like aerospace, automotive, and medical devices.
Addressing these challenges requires a combination of advanced technology, skilled labor, and meticulous planning and execution . . . like the team at Precision Bending.
Contact us today to find our more about our team and our process.