Precision Bending for Charge Air Cooler (CAC) Tubes
Precision tube bending is an essential process in the fabrication of customized Charge Air Cooler (CAC) tubes, which play a critical role in enhancing the efficiency and performance of various cooling systems, particularly in automotive and industrial applications.
This specialized technique involves shaping metal tubes without compromising their diameter or structural integrity, ensuring that the tubes can efficiently manage thermal stress and pressure differentials during operation.
The Need for Precision in Tube Bending
Charge Air Coolers are crucial for reducing the temperature of the air entering the engine's intake manifold. This process helps to improve combustion efficiency and reducing emissions.
The CAC tubes must navigate complex paths and connect multiple components within constrained spaces. Due to this complexity, specialized tubing is needed. Precision tube bending allows for the creation of exact bends and curves necessary to meet specific design requirements, avoiding issues such as crimping or wrinkling, which can impede airflow and diminish performance.
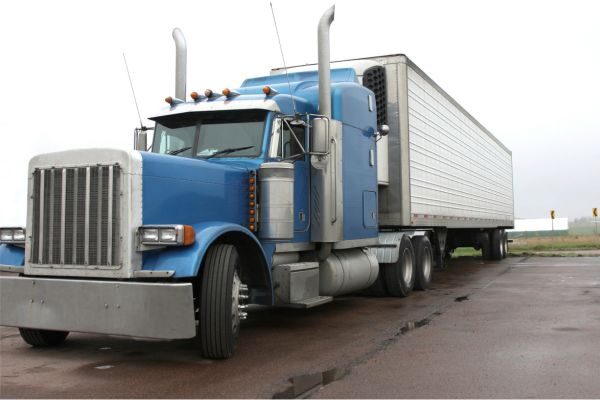
Bending Techniques and Tooling
For get the finished product needed for a CAC tube, the process of precision tube bending involves several techniques and advanced technologies. Typically, it starts with CNC (Computer Numerical Control) tube bending machines, which offer high levels of accuracy and repeatability. CNC bending machines use pre-programmed instructions to manipulate the tube along multiple axes, achieving complex geometries with tight tolerances.
Another crucial aspect of precision tube bending is the selection of appropriate tooling. The use of mandrels and wiper dies is common; these tools support the tube internally and externally during the bending process. This process helps prevent flattening or ovalization of the tubing.
Mandrels are particularly important when working with thin-walled tubes used in CAC applications, as they help maintain the circular cross-section necessary for optimal airflow.
Material Considerations
The choice of material or metal for CAC tubes is also significant in precision tube bending process. Materials typically used include aluminum and stainless steel, which offer an excellent balance of lightweight properties, corrosion resistance, and thermal conductivity.
Each material behaves differently under stress and requires specific adjustments during the bending process, such as heat treatments or specific bend radii, to avoid material fatigue or cracking.
Customization and Prototyping
For customized CAC tubes, the design and prototyping phases are critical. Engineers must consider factors for precision bending such as the intended placement within the assembly, connection points, and the overall thermal dynamics of the system.
3D modeling software plays a crucial role here, allowing designers to simulate and adjust the tube paths before actual production. This digital step is vital to ensure that the final product perfectly matches the design specifications and fits seamlessly into its designated position without requiring further modifications.
Quality Control and Testing
Once the tubes are bent, rigorous quality control and testing are essential. This may include dimensional verification, visual inspection, and performance testing under simulated operating conditions. Non-destructive testing methods, such as photogrammetric testing or X-ray imaging, are often used to detect any internal defects or weaknesses in the bends.
Precision tube bending for customized CAC tubes is a highly specialized field that combines advanced manufacturing techniques, meticulous material selection, and rigorous testing to ensure optimal performance.
As industries continue to demand more efficient and compact cooling solutions, the role of precision in tube bending becomes increasingly critical, underscoring the need for expertise, precision machinery, and continuous innovation in this field.
If you have a custom bending project that needs to have tightly engineered specification and quality delivery, contact the Precision Bending team.